Вихретоковые матрицы. Испытание дефектоскопа Reddy (Eddyfi) в Руслаб
Практические испытания вихретокового дефектоскопа Reddy с преобразователем Sharck, разработанный канадской компанией Eddyfi для контроля трещин в объектах контроля в нефтегазовой, энергетической и авиакосмической и других отраслях промышленности.
Контроль образца 2
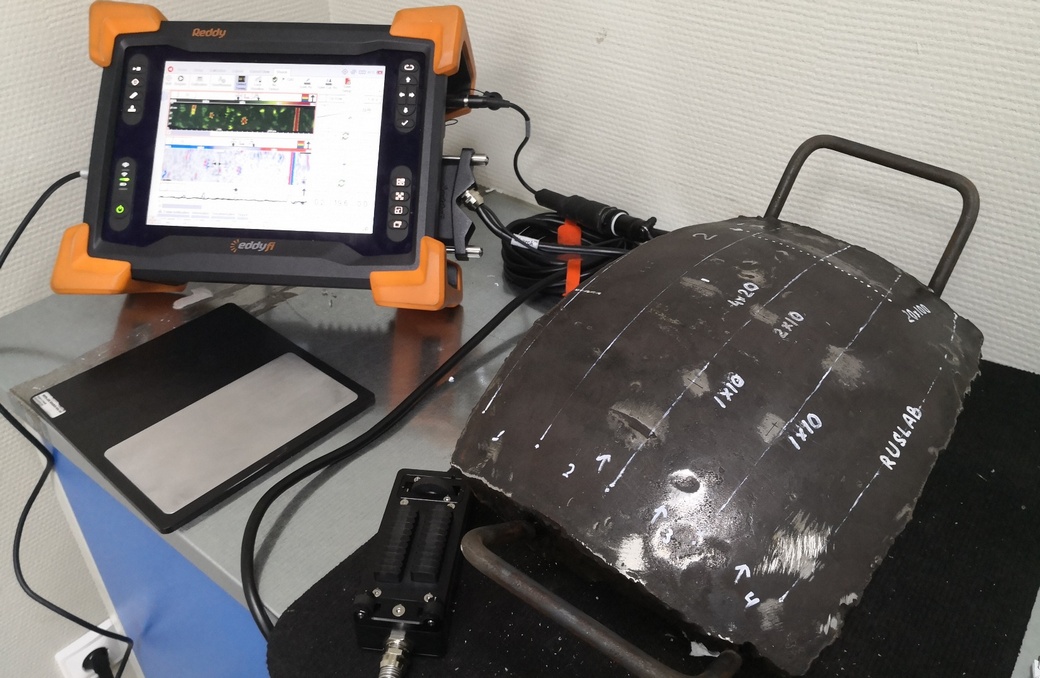
Для испытаний прибора Reddy с преобразователем Sharck на вихретоковой тангенциальной матрице был предоставлен Образец 2. Материал образца – сталь углеродистая литая. Образец является фрагментом задвижки, находившегося в эксплуатации. На образец нанесены искусственные дефекты в виде прорезей различной глубины и длины. Сбор данных производился на территории Русской лаборатории. Анализ данных проводился в офисе ПЕРГАМ-ИНЖИНИРИНГ.
Характеристики преобразователя:
- Топология: Тангенциальная;
- Ширина охвата: 53 мм;
- Количество сканирующих элементов с катушками (по 3 катушки в элементе): 22 (11 × 2 ряда);
- Минимальное количество требуемых каналов: 64;
- Частота (настроенная и зафиксированная): 20 кГц и 80 кГц (двух частотный режим работы);
- Разрешение датчика пути: 20.53 считываний/мм;
- Минимальный/максимальный диаметры кривизны поверхности: 25,4 см/40,6 см.
Перед началом испытания Образец 2 был размечен на 4 вертикальные и 2 горизонтальные полосы для сканирования. Полосы пронумерованы в порядке возрастания 1-4 - вертикальные, 5 и 6 - горизонтальные.
Рисунок 3. Вертикальная разметка поверхности Образца 2 и схема сканирования.
Полоса сканирования 1
Преобразователь Sharck откалиброван по стандартной процедуре, рекомендованной производителем. Для того, чтобы обеспечить сцепление датчика пути с поверхностью образца (запись координат пройдённого пути), сканирование полосы 1 производилось в направлении от дальнего края образца в сторону оператора (см. рисунок 3). При сканировании, датчик пути располагался во внутренней части образца, а кабель преобразователя – с левого края образца.
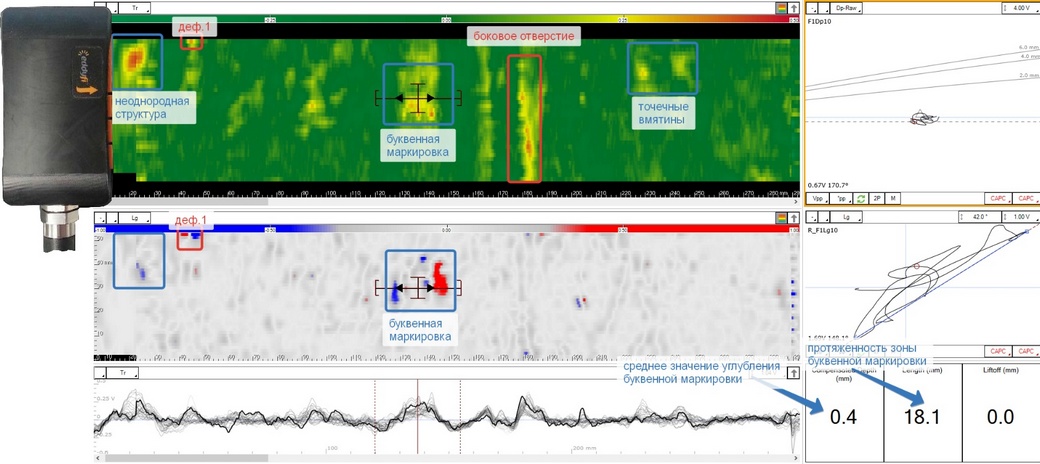
- верхнее окно: Tr.С-скан. Используется для визуализации поперечных трещин;
- верхнее правое окно: Dp-Raw.Кривая Лиссажу. Представляет собой необработанный сигнал на импедансной плоскости каналов в зоне перекрестия курсора на С-скане. Используется для измерения глубины трещин;
- нижнее окно: Lg.С-скан. Используется для быстрой локализации продольных трещин;
- нижнее правое окно Lg.Кривая Лиссажу. Представляет собой сигнал продольных каналов под курсором на Lg.C-скане.
В зоне полосы 1 на образце визуально наблюдаются:
- дефекты поверхности;
- буквенная маркировка, выполненная клеймением;
- имитация подповерхностного дефекта (боковое отверстие на глубине ≈4 мм);
- при разметке в зону попал левый край искусственного дефекта 1 в виде длинной прорези.
На представленных данных сканирования полосы 1 (Рисунок 4) видно, что общая чувствительность контроля позволяет обнаружить:
- левый край дефекта 1 (индикация дублируется Tr.С-сканом и Lg.С-сканом);
- буквенное клеймение (индикация дублируется Tr.С-сканом и Lg.С-сканом), измерена площадь зоны ≈(19,1х18,1) мм и глубина тиснения ≈0,4мм;
- подповерхностный дефект (боковое отверстие) на Tr.С-скане, который является поперечным к направлению сканирования, но необходимо отметить, что боковое отверстие — это объемный тип дефекта. Выявление объемных типов дефектов является профилем других вихретоковых матриц из линейки Eddyfi.
На Tr.С-скане визуализированы так же дефекты поверхности: вмятины и неоднородности.
Полоса сканирования 2
Сканирование полосы 2 проводилась в направлении от оператора в сторону дальнего края образца (см. рисунок 3).
В зоне полосы 2 на образце визуально наблюдаются:
- забоины и неоднородности;
- имитации трещин: дефекты 1, 2 (полностью) и левый край дефекта 3 и 4 захвачены разметкой. Все дефекты имеют поперечную ориентацию к оси сканирования.
На представленных данных сканирования полосы 2 (Рисунок 5а) видно, что общая чувствительность контроля позволяет обнаружить:
- искусственные дефекты 1 и 2 и дефекты поверхности хорошо выявляются (индикации дублируется Tr.С-сканом и Lg.С-сканом), измерен дефект 2: глубина 3,4 мм, протяженность 21,3 мм.
- левый край дефектов 3 и 4 выявляется только на Lg.С-скане, так как ширина полосы выборки данных для генерации получении Tr.С-скана немного уже, поэтому дефекты не захватываются. Это может быть учтено в дальнейшем при разметке объекта контроля. Ширина разметки при использовании Tr.С-скана - 44 мм.
- забоины и неоднородности.
В результате оптимизации данных сканирования полосы 2 (Рисунок 5б) видно:
- отфильтрованы все шумы и ненужные сигналы;
- все индикации дефектов остались;
- дополнительно измерена глубина дефекта 1: 2,7 мм.
Рисунок 5. а – данные полученные с прибора. б – данные после оптимизации.
Полоса сканирования 3
Сканирование полосы 3 производилось в направлении от оператора в сторону дальнего края образца (см. рисунок 6).
В зоне полосы 3 на образце визуально наблюдаются:
- забоины и неоднородности;
- имитации трещин: поперечных дефект 1 (полностью), правые края поперечных дефектов 3 и 4 захвачены разметкой, продольный дефект 5 (полностью).
- небольшие вмятины и неоднородности.
На представленных данных сканирования полосы 3 (Рисунок 6) уже применена оптимизация и отфильтрованы все ненужные сигналы и шумы. При анализе данных видно:
- поперечный дефект 1 и правый край дефекта 3 (индикации дублируется Tr.С-сканом и Lg.С-сканом);
- правый край поперечного дефекта 3 только на Lg.С-скане, так как ширина полосы выборки данных для генерации получении Tr.С-скана немного уже, поэтому дефекты не захватываются. Это может быть учтено в дальнейшем при разметке объекта контроля. Ширина разметки при использовании Tr.С-скана - 44 мм
- продольный дефект 5 выявляется только Lg.С-сканом. Измерены его параметры: глубина 0,8 мм и протяженность 11,3 мм. Алгоритм обработки и построения Tr.С-скана предназначены только для выявления поперечных дефектов, поэтому индикации продольной трещины 5 на Tr.С-скане отсутствует.
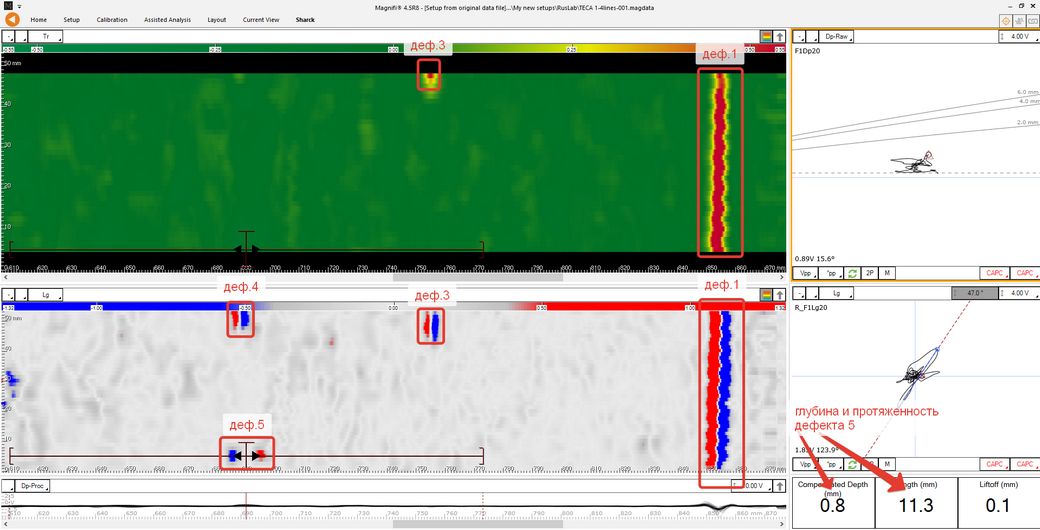
Для визуализации продольных трещин применяется DP-Proc C-скан. DP-Proc C-скан особый математический алгоритм обработки данных контроля. Виды сканов могут легко переключаться в процессе сбора данных или при анализе. Рассмотрение контроля и визуализации продольных трещин продолжится для при анализе данных полос сканирования 5 и 6.
Полоса сканирования 4
Сканирование полосы 4 производилось в направлении от оператора в сторону дальнего края образца (см. рисунок 7).
В зоне полосы 4 на образце визуально не наблюдаются дефекты. Зона полосы 4 сканировалась дважды:
- первое сканирование произведено, для того чтобы убедиться в отсутствие дефектов (рисунок 7а);
- второе сканирование производилось после воздействия на поверхность сильного постоянного магнита: длительность воздействия около 60 сек (рисунок 7б).
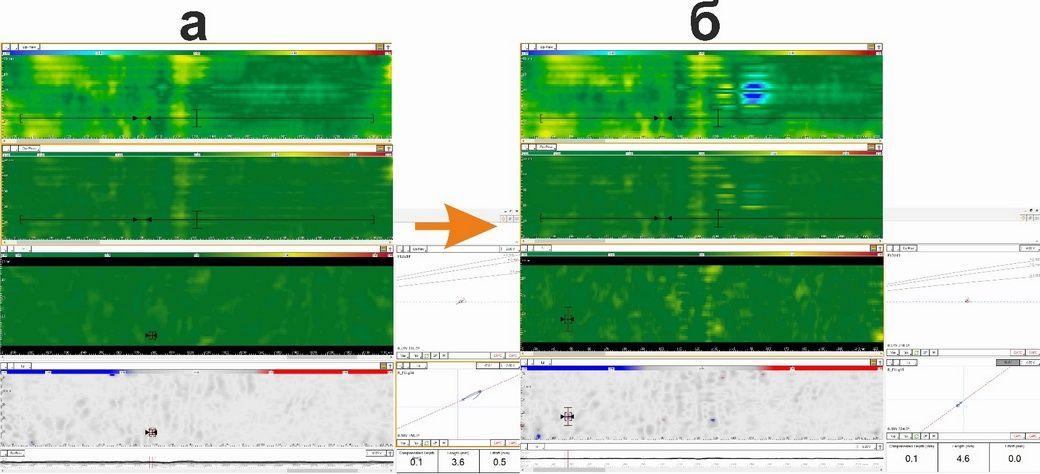
На рисунке 7 видно, что влияние намагниченной зоны сканирование ничтожно. Индикация намагниченной точки проявляется только на Dp-Raw.С-скан (верхний скан, рисунок 7б). Dp-Raw.С-скан является массивом «сырых» (необработанных) сигналов импеданса. Dp-Raw.С-скан чаще всего не используется при анализе данных и измерении дефектов. Dp-Raw.С-скан мало участвует в оценке параметров дефектов.
Стоит отметить, что для полноты эксперимента необходимо произвести намагничивание зоны образца с трещиной и произвести дополнительный сбор данных для оценки влияния локальной намагниченности на качество отображения индикации дефекта.
Представленные четыре вида С-сканов на рисунке с верху вниз представляют собой:
- Dp-Raw. С-скан. Является массивом необработанных сигналов импеданса. Исходные данные;
- Dp-Proc. С-скан. Используется для визуализации осевых трещин с компенсацией магнитной проницаемости материала и уровня зазора. Каждая горизонтальная линия соответствует каналу преобразователя.
- Tr.С-скан. Используется для визуализации поперечных трещин Строиться путем наложения полосовых диаграмм поперечных каналов;
- Lg.С-скан. Используется для быстрой локализации продольных трещин.
Рисунок 8. Горизонтальная разметка поверхности образца 2 и схема сканирования.
Полоса сканирования 5
Сканирование полосы 5 производилось слева на право (см. рисунок 8).
В зоне полосы 5 на образце визуально наблюдаются:
- имитации трещин: продольный дефект 4, поперечный дефект 5;
- небольшие вмятины и неоднородности.
На представленных данных сканирования полосы 5 (Рисунок 9) уже применена оптимизация и отфильтрованы все ненужные сигналы и шумы. При анализе данных обнаружилось, что балансировка преобразователя перед сканированием полосы 5 была выполнена некорректно, продольная и поперечная трещины на скане в середине рисунка 9 имеют слабые индикации.
Несмотря на некорректную балансировку, данные обладают достаточным качеством, чтобы произвести правильную оценку дефектов. В верхней части рисунка 9 приведен Tr.С-скан, на котором отображается индикация поперечного дефекта.
В дополнение к окну с Lg.С-сканом вызвано окно с Lg.Ленточная диаграммой (в самом низу рисунка 9). Lg.Ленточная диаграмма позволяет сопоставить показания с Lg.С-скан при определении краев продольной трещины. Первый край продольной трещины всегда начинается с отрицательного значения: пик на Lg.Ленточная диаграмма или синий цвет на Lg.С-скане.
Для сравнения: поперечный дефект начинается с положительного пика Lg.Ленточная диаграмма или красный цвет на Lg.С-скане. Дефект 4 был дополнительно измерен: глубина дефекта 0,5 мм, протяженность – 10,6 мм.
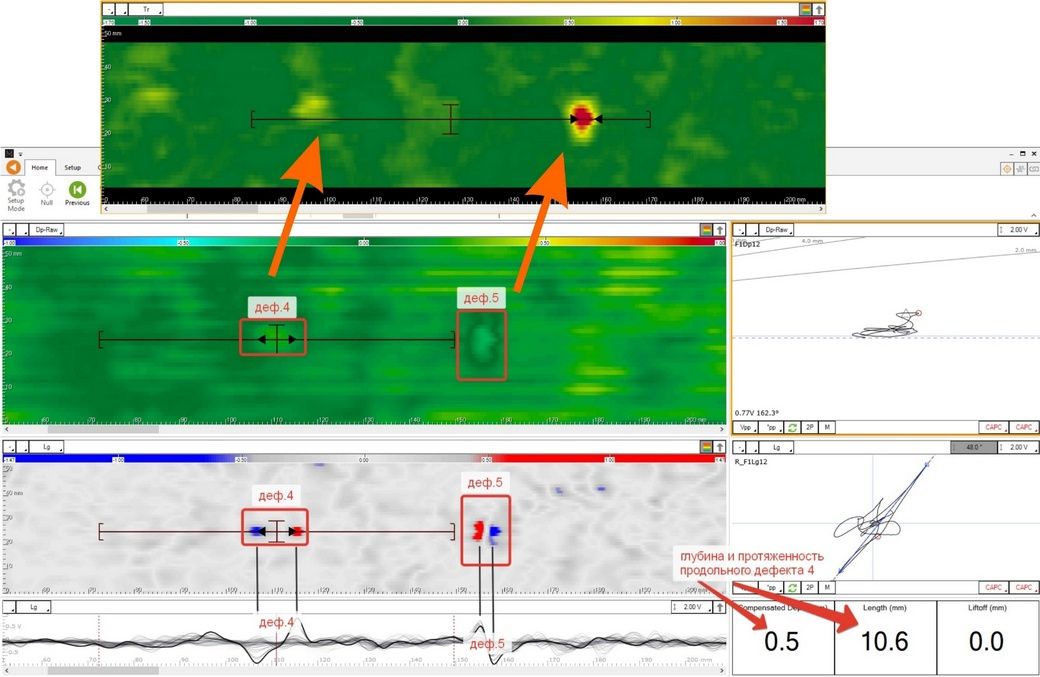
На изображении представлены:
- первое верхнее окно: Tr.С-скан. Используется для визуализации поперечных трещин. Строиться путем наложения полосовых диаграмм поперечных каналов;
- второе окно слева: Dp-Raw. С-скан. Является массивом необработанных сигналов импеданса. Исходные данные;
- третье окно слева: Lg.С-скан, который используется для быстрой локализации продольных трещин;
- четвертое слева: Lg.Ленточная диаграмма: полосовые диаграммы продольных каналов. Используется для точной локализации продольных трещин.;
- верхнее окно справа: Dp-Raw.Кривая Лиссажу. Представляет собой необработанный сигнал на импедансной плоскости каналов в зоне перекрестия курсора на С-скане. Используется для измерения глубины трещин;
- нижнее окно справа: Lg.Кривая Лиссажу, которая представляет сигнал продольных каналов под курсором на Lg.C-скане.
Полоса сканирования 6
Сканирование полосы 6 производилось слева на право (см. рисунок 10).
В зоне полосы 6 на образце визуально наблюдаются:
- имитации трещин: продольные дефект 2 и 3;
- буквенная маркировка, выполненная клеймением.
На представленных данных сканирования полосы 6 (Рисунок 10) уже применена оптимизация и отфильтрованы все ненужные сигналы и шумы. Обе продольные трещины выявлены. На рисунке видно, что для этого использовалась комбинация окон Dp-Proc. С-скан и Lg.С-скан, которые предназначены для визуализации продольных трещин.
Для примера приведен Tr.С-скан, на котором нет отображений продольных дефектов. В дополнение к окну с Lg.С-сканом вызвано окно с Lg.Ленточная диаграммой (в самом низу рисунка 10). Lg.Ленточная диаграмма позволяет сопоставить показания с Lg.С-скан при определении краев продольной трещины. Первый край продольной трещины всегда начинается с отрицательного значения: пик на Lg.Ленточная диаграмма или синий цвет на Lg.С-скане.
Дефект 2 был дополнительно измерен: глубина дефекта 4,2 мм, протяженность – 19,8 мм.
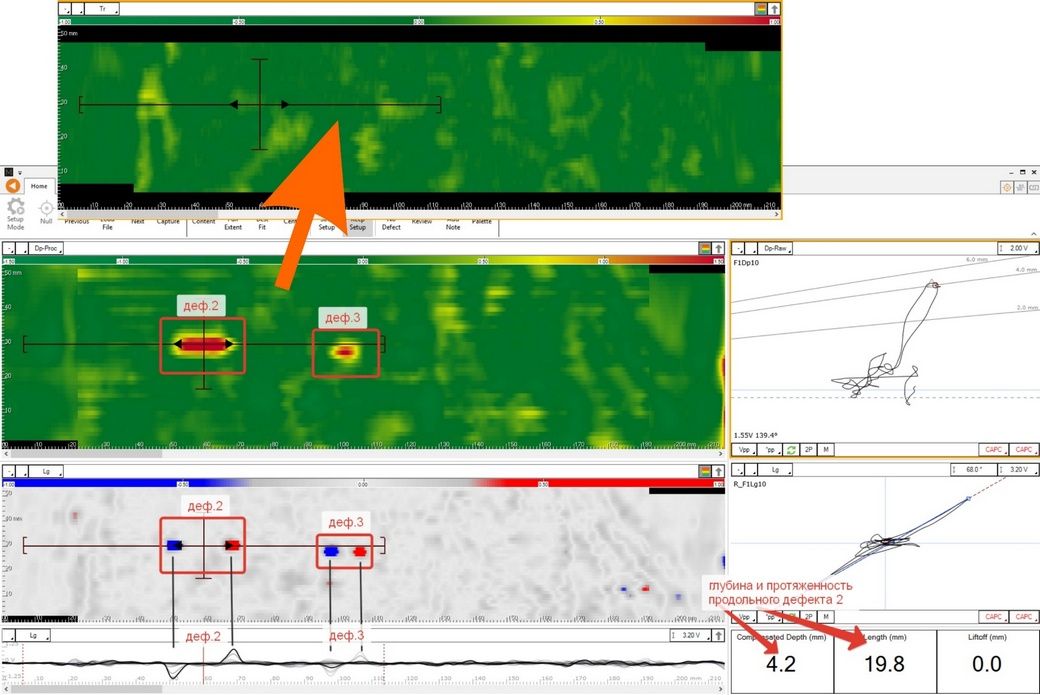
На изображении представлены:
- первое верхнее окно: Tr.С-скан. Используется для визуализации поперечных трещин. Строится путем наложения полосовых диаграмм поперечных каналов;
- второе окно слева: Dp-Proc. С-скан. Предназначен для визуализации осевых трещин с компенсацией магнитной проницаемости материала и уровня зазора. Каждая горизонтальная линия соответствует каналу преобразователя;
- третье окно слева: Lg.С-скан, который используется для быстрой локализации продольных трещин;
- четвертое слева: Lg.Ленточная диаграмма: полосовые диаграммы продольных каналов. Используется для точной локализации продольных трещин.;
- верхнее окно справа: Dp-Raw.Кривая Лиссажу. Представляет собой необработанный сигнал на импедансной плоскости каналов в зоне перекрестия курсора на С-скане. Используется для измерения глубины трещин;
- нижнее окно справа: Lg.Кривая Лиссажу, которая представляет сигнал продольных каналов под курсором на Lg.C-скане.
Контроль образца 1
Рисунок 11. Схема сканирования образца 1.
Для испытаний прибора Reddy с преобразователем I-flex (Рисунок 12) на гибкой вихретоковой матрице был предоставлен Образец 1 (Рисунок 11). Материал образца – сталь углеродистая литая. Образец является фрагментом изделия, находившегося в эксплуатации. На образец нанесены искусственные дефекты в виде прорезей различной глубины и длины.
Сбор данных производился на территории Русской лаборатории. Анализ данных проводился в офисе ПЕРГАМ ИНЖИНИРИНГ.
Рисунок 12. Характеристики преобразователя:
- Топология: импедансная, single driver, short, double driver;
- Ширина охвата: 56 мм;
- Количество катушек: 48;
- Диаметр катушек: 3,5 мм»
- Минимальное количество требуемых каналов: 64;
- Диапазон частот : 50-525 кГц;
- Центральная частота 250 кГц;
- Глубина проникновения до 2 мм;
- Минимально выявляемая длина дефекта: 1 мм.
На образце 1 в зоне контроля визуально наблюдаются:
- искусственные дефекты;
- зернистая структура металла.
Поверхность удовлетворяет требования вихретокового контроля
В отсутствие калибровочного образца из того же материала, что и объект испытаний, преобразователь I-flex настраивался непосредственно на поверхности образца 1. Образец 1 сканировался от центра в двух направлениях, как это показано на рисунке 11. Вследствие сложной геометрической формы образца 1 невозможно применить датчик пути, поэтому сканирование производилось с синхронизацией по времени.
На представленных данных (Рисунки 13 и 14) результаты контроля 1 и контроля 2. Отображение информации производится на С-скане продольного считывания (верхняя часть экрана на рисунках 13 и 14) и С-скане поперечного считывания (нижняя часть экрана на рисунках 13 и 14).
При анализе данных на рисунках видно:
- все дефекты выявлены несмотря на переменную геометрию поверхности;
- произвольно выбраны дефектов 1 и 5 и измерена их протяженность: 17,8 мм и 30,9 мм соответственно;
- высокая чувствительность матрицы позволяет наблюдать зернистую структуру металла (слабая рябь в различных оттенках зеленого).
Рисунок 13. Сканирование 1 преобразователем I-flex.
Рисунок 14. Сканирование 2 преобразователем I-flex.